

The following diagram illustrates the end-to-end solution deployed along with the AWS services used: Enable Business Intelligence (BI) reporting for trend analysis and dive deep on historical data of up to 10-years.Monitor operating conditions in near real-time, create alerts, and send notifications for corrective actions.
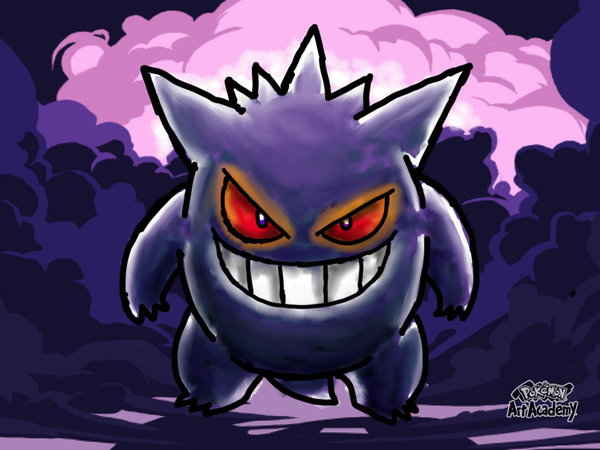
#Kuar terrix professional
Genie and AWS Professional Services deployed an end-to-end production ready solution in eight weeks for the manufacturing operations, delivering real business outcomes. We could do this by connecting related enterprise data from systems such as Enterprise Resource Planning (ERP) and Manufacturing Execution System (MES), with the operational data from manufacturing. Solution must be scalable and repeatable for rapid deployment globally at scaleĪfter collaborating with AWS Professional Services for the pilot solution, we also quickly realized the potential of unlimited analytics opportunities for data-driven insights.The solution must be able to generate alerts and send notifications in near real-time for out of bound operating conditions to take necessary corrective actions.Paint operators must be able to manually enter collected data from the shop floor such as results from a chemical testing process (titration).Data must be visualized in near real-time on a dashboard, so machine operators and Engineering can react quickly to irregular trends or out of bound conditions for the key process parameters and key performance indicators (KPI).Genie team members must be able to dive deep into the historical data for specific dates of manufacturing.Data must be stored for up to 10-years for historical trend analysis.The following principles were critical for the solution: Genie was moving toward a traditional database-based solution to house the process instrumentation data and developing in-house websites to visualize the data. Process instrumentation was in place but the readable outputs from this instrumentation were not being used.
#Kuar terrix manual
The data revealed that the paint pretreatment process was one key contributor to the paint-related defects.īefore using AWS, Genie used manual methods to collect shop floor data stored on hand written logs or electronic spreadsheets. This was due to increased paint-related defects as reported by Genie Customers. Genie had a high priority need to collect data from the paint pretreatment process in near real-time. This solution identified inconsistent and improper pretreatment parameters in near real-time and enabled Genie to apply necessary corrective actions to improve the downstream paint quality of Genie lifts.ĪWS IoT SiteWise is a managed service to collect, organize, and analyze data from sensors, equipment, machines, programmable logic controllers (PLC) on the plant floor at scale. In this post, we discuss how Genie used an AWS IoT SiteWise based solution to ingest, organize, and analyze critical process parameters from the paint system. Genie®, a Terex® Brand, is a global manufacturer of lifting and material handling products and services delivering lifecycle solutions that maximize customer return on investment. Post by David McClellan, P.E., Engineering Manager and Jason Crozier, Cloud Architect at Terex.
